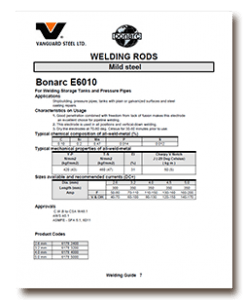
Quick Link
Download your FREE copy
Vanguard Steel has been supplying welding consumables for over 30 years under the Trade name BonarcTM. Manufactured in Korea, we are able to control quality and consistency which sets us apart from our competition. Our welding consumables are CWB & CSA approved.
With the success of the BonarcTM line, Vanguard Steel has added our VGD WireTM. Branded to take advantage of our increasing reputation for outstanding Quality and Value this wire has established a good reputation in the market. VGD WireTM has made an immediate impact. From the quality of the helix to the consistency of the arc, VGD wire has given the industry an additional choice. These welding consumables are also CWB & CSA approved
Click on booklet to view content
Mild steel electrodes are welding electrodes that are specifically designed for use on mild or low-carbon steels. These electrodes are typically made of a mild steel core wire coated with flux. The flux coating helps to protect the weld area from contamination and also provides shielding from the atmosphere during the welding process.
Mild steel electrodes are commonly used in the construction, manufacturing, and repair industries, as well as in automotive and shipbuilding applications. They are suitable for welding a variety of mild steels, including those with low carbon content.
When selecting a mild steel electrode, it is important to consider the thickness of the material being welded, the type of joint being made, and the welding position. Different types of mild steel electrodes are available for different applications, such as general-purpose electrodes, low hydrogen electrodes for high-strength applications, and cellulose-coated electrodes for vertical-up welding.
Overall, mild steel electrodes are a versatile and cost-effective option for welding mild or low-carbon steels in a variety of applications.
Type of Rod | Typical Applications | Specification |
6010 | Covering is low hydrogen, iron powder; common of welding applications include 71 ksi (490 MPa) class high tensile strength steels found in structural steels for buildings, bridge construction, storage tank fabrication, ship building, industrial and mining machinery fabrication. | CWB to CSA W48-14 Classification: E431 0 AWS/ASME A5.1 – 04 E6010 |
6011 | Covering is high cellulose type; common applications include welding of storage tanks, pipe, pressure vessel fittings, steel sheets, piping and ship construction. | AC & DC C.W.B. to CSA W48.1 AWS A5.1 ASMFE – SFA 5.1, 6011 |
6013 | For Light Structural Steel Applications Welding of all kinds of light constructional work in all positions, including pipe welding. | CWB to CSA W48-14 Classification: E4313 AWS/ASME A5.1 – 04 E6013 |
7014 | Covering is iron powder, Titania type; common welding applications include fillet welding of structural steels for buildings, bridge, ship structures and general structures. | CWB to CSA W48-14 Classification: E4914 AWS/ASME A5.1 – 04 E7014 |
7018 | For Highly Efficient Welding of 500N/mm2 Class High Tensile Steel. Applications Welding of mild steel and 500N/mm2 class high tensile steel of ships, bridges, storage tanks, buildings, industrial machinery and mining machinery. Covering is low hydrogen, iron powder; common of welding applications include 71 ksi (490 MPa) class high tensile strength steels found in structural steels for buildings, bridge construction, storage tank fabrication, ship building, industrial and mining machinery fabrication. | CWB to CSA W48-14 Classification: E4918-1-H8 AWS/ASME A5.1 – 04 E7018-1 |
7018-1 | For Aluminum-killed Steel for Low Temperature Applications Covering is low hydrogen, iron powder; common of welding applications include 71 ksi (490 MPa) class high tensile strength steels found in structural steels for buildings, bridge construction, storage tank fabrication, ship building, industrial and mining machinery fabrication. | CWB to CSA W48-14 Classification: E4918-1-H8 AWS/ASME A5.1 – 04 E7018-1 |
7024 | For Highly Efficient Fillet Welding Applications Horizontal and flat welding of ship structures, bridges, structural steels for buildings and general structures. | CWB to CSA W48-14 Classification: E4924 AWS/ASME A5.1 – 04 E7024 |
Mild steel MIG wire is a type of welding wire
Mild steel MIG wire is a type of welding wire used in the process of MIG welding. MIG welding, or metal inert gas welding, is a type of welding that uses a wire electrode to fuse two pieces of metal together. The wire electrode is fed through a MIG welding gun and is used to create an arc between the welding gun and the metal being welded.
Mild steel MIG wire is used for welding mild steel, which is a low-carbon steel that is relatively easy to work with. It is commonly used in manufacturing, construction, and other industries where a strong, durable weld is needed. Mild steel MIG wire comes in a variety of diameters, ranging from 0.023 inches to 0.045 inches, and is available in both solid and flux-cored versions.
When selecting a mild steel MIG wire, it is important to consider the thickness of the metal being welded, the type of shielding gas being used, and the desired weld strength. It is also important to choose a wire that is compatible with the welding equipment being used, as different machines may require different types of wire.
flux core welding wire is tubular and inside the tube is flux
Mild steel flux-cored wire is a type of welding wire used in a welding process called Flux-Cored Arc Welding (FCAW). This type of wire contains a flux inside the wire that shields the weld from the atmosphere, preventing contamination and ensuring a high-quality weld. The wire is designed to weld mild steel, which is a low-carbon steel with a carbon content of approximately 0.05% to 0.25%.
Mild steel flux-cored wire is commonly used in various applications such as shipbuilding, structural steel fabrication, pipeline welding, and heavy equipment repair. The wire is ideal for welding thick materials and can be used in all welding positions.
When using mild steel flux-cored wire, it’s important to select the appropriate wire diameter and welding parameters to achieve the desired weld quality. Additionally, safety precautions such as wearing proper personal protective equipment (PPE) should be taken to ensure the safety of the operator.
Metal Core is tubular with majority of powder core iron, with varying amounts of other substances added in
Metal core welding wire is a type of welding wire used in the process of welding. It is made up of a metal core surrounded by a flux coating that protects the weld from contamination and oxidation. The metal core of the wire is typically made of a high-strength alloy, such as stainless steel or nickel alloy, and the flux coating can be made of various materials depending on the specific welding application.
Metal core welding wire is popular because it allows for higher welding speeds and better penetration compared to other types of welding wire. It also produces a smooth, consistent weld bead with minimal spatter. Metal core welding wire is commonly used in industries such as construction, automotive, aerospace, and manufacturing.
When selecting a metal core welding wire, it is important to consider the specific requirements of the welding application, such as the type of base metal, welding position, and desired weld quality. It is also important to choose a wire that is compatible with the welding equipment being used.
Stainless steel electrodes welding rods are consumable electrodes
Stainless steel electrodes welding rods are consumable electrodes used for welding stainless steel. These electrodes are made of a core wire, which is usually made of stainless steel, and a flux coating, which is designed to protect the weld pool from atmospheric contamination and also to provide additional alloying elements to the weld metal.
Stainless steel electrode welding rods are available in different sizes and types, each designed for specific applications. For example, there are electrodes designed for welding austenitic stainless steels, which have a high nickel content, as well as those designed for welding ferritic and martensitic stainless steels, which have a lower nickel content.
When using stainless steel electrode welding rods, it is important to select the right type of electrode for the specific application and to follow the manufacturer’s instructions for proper use. Additionally, the welder must take steps to ensure that the weld area is clean and free of contaminants, as well as to maintain the proper arc length and travel speed during the welding process.
Stainless steel MIG wire is specifically designed for welding stainless steel
Stainless steel MIG wire is a type of welding wire used in the process of metal inert gas (MIG) welding. MIG welding is a technique that uses a continuous, consumable electrode wire to join two or more metal parts together. The electrode wire is fed through a welding gun and is melted by an electric arc, which fuses the wire and the base metal together.
Stainless steel MIG wire is specifically designed for welding stainless steel. It is made from high-quality stainless steel and contains a certain amount of chromium and nickel, which gives it excellent corrosion resistance and high-temperature strength. The wire is available in various diameters and grades, depending on the type of stainless steel being welded and the application requirements.
Stainless steel MIG wire is commonly used in the fabrication of structures, pipes, tanks, and other components that require high corrosion resistance and durability. It is also used in the food and beverage industry, as well as in the pharmaceutical and chemical industries, where hygiene and cleanliness are critical factors.
Stainless steel flux-cored welding wire is a type of welding wire used in the process of flux-cored arc welding
Stainless steel flux-cored welding wire is a type of welding wire used in the process of flux-cored arc welding (FCAW). It is designed to be used with a flux-cored welding gun and is used for welding stainless steel.
The flux-cored wire contains a flux that protects the molten metal from contamination by the atmosphere, providing a shield around the weld pool. The flux also helps to remove impurities from the weld and can improve the appearance of the finished weld.
Stainless steel flux-cored welding wire is typically used in applications where a high-quality weld is required, such as in the food and beverage industry, pharmaceuticals, and petrochemicals. It is also used in applications where the welded joint will be exposed to corrosive environments.
When selecting a stainless steel flux-cored welding wire, it is important to choose one that is compatible with the base metal being welded and the welding process being used. The wire should also be chosen based on the specific application and the desired properties of the finished weld.
Hard surfacing wire, also known as welding wire or filler metal
Hard surfacing wire, also known as welding wire or filler metal, is a type of wire that is used in welding applications to provide a protective layer over a surface to increase its hardness, durability, and resistance to wear and tear.
Hard surfacing wire is made of various materials, such as carbon steel, stainless steel, nickel alloys, or cobalt alloys, depending on the specific application requirements. The wire is typically fed through a welding torch or gun, where it is melted and applied to the surface being welded.
The choice of hard surfacing wire depends on the specific application and the type of base material being welded. Some common types of hard surfacing wire include:
Flux-cored wire: This type of wire is used in welding applications where a flux coating is necessary to protect the weld from atmospheric contaminants.
Gas-shielded wire: This type of wire is used in applications where a protective gas is needed to prevent oxidation during the welding process.
Metal-cored wire: This type of wire is used in applications where a high deposition rate is required, and it provides a more stable arc and better penetration.
Submerged arc wire: This type of wire is used in applications where a high deposition rate and deep penetration are required, and it is ideal for welding thick materials.
Hard surfacing wire is commonly used in industries such as mining, construction, agriculture, and manufacturing, where equipment and machinery are subject to heavy wear and tear.
Brand Name | Dia mm (in) | Typical Chemical Composition of all-welding-metal (%) |
||||
C | Si | Mn | Cr | Mo | ||
K250HT | 1.2 (.045) 1.6 (.062) | 0.07 | 0.5 | 1.59 | 1.3 | |
K300HT | 1.2 1.6 | 0.09 | 0.68 | 1.54 | 1.1 | |
K350HT | 1.2 1.6 | 0.12 | 0.45 | 1.37 | 1.3 | 0.2 |
K450HT | 1.2 1.6 | 0.24 | 0.51 | 1.2 | 2 | 0.6 |
K600HT | 1.2 68362012 1.6 68362016 | 0.25 | 2.18 | 0.36 | 6.5 | 0.03 |
K700HT | 1.2 1.6 | 0.3 | 2.4 | 0.5 | 7.0 | W:0.7 |
K800HT | 1.2 1.6 | 0.44 | 1.5 | 0.55 | 8.6 | W:0.5 |
Welding spatters on 70S6 wire can be caused by several factors such as improper welding technique, incorrect voltage or amperage settings, or a contaminated workpiece or wire. Here are some possible solutions to reduce welding spatters on 70S6 wire:
Check your welding technique: Welding spatters can occur if you’re using improper welding technique. You should maintain a consistent travel speed and angle, as well as a steady stick-out length. Welding too slowly can cause the wire to overheat and create more spatter. On the other hand, welding too fast can cause the weld bead to be insufficiently penetrated, leading to more spatters.
Adjust voltage and amperage settings: Incorrect voltage or amperage settings can also lead to welding spatters. Make sure you are using the correct settings for your specific welding application. Lower voltage and amperage settings can also reduce spatters.
Clean the workpiece and wire: Make sure the workpiece and wire are clean and free from any oil, rust, or other contaminants. Use a wire brush or grinder to remove any surface contamination before welding.
Use a spatter-reducing agent: You can also use a spatter-reducing agent to reduce welding spatters. These agents help prevent spatters from sticking to the workpiece and wire by creating a barrier between the two.
Use a different wire: If the above solutions don’t work, consider using a different type of wire that is more suited to your welding application.
Remember that welding spatters can be hazardous, so always wear proper protective equipment like welding gloves, helmets, and clothing.
Fault or defect:
Poor Weld Starts
Probable cause:
Voltage too low.
Too much stick out (stubbing).
Wire not clipped on an angle (stubbing).
Excessive Spatter
Voltage too low.
Change gas selection ( from CO-2 to Steelmix ) Change polarity.
Burn Through
Current too high.
Travel speed too slow.
Too large a gap
ChangE gas section ( from CO-22 to Steetmix )
Convex Bead
Voltage/current too low.
Too much stick out.
Voltage loss due to poor connections.
Test results should not be assumed to be the expected results in a particular application or weldment. Actual results will vary depending on many factors, including, but not limited to, weld procedure, plate chemistry and temperature, weldment design and fabrication methods. Users are cautioned to confirm by qualification testing, or other appropriate means, the suitability of any welding consumable and procedure before use in the intended application.
After manufacturing Bonarc stainless steel electrodes are packaged in re-sealable plastic bags, then inserted in plastic sleeves. These plastic sleeves provide protection from damage and moisture.
When stored under normal conditions the electrodes will very slowly pick up moisture.
5-15 °C (41-59°F) – Relative humidity ::
5 60% 15-25°C (59-77°F) – Relative humidity ::5 50%
25°C (> 77°F) – Relative humidity ::5 40%
Prior to leaving the factory the humidity level of all Bo narc stainless steel electrodes are verified. If during storage the electrodes do pick up moisture/humidity re-drying of the electrodes is an easy method to correct this “issue”.
Bonarc stainless steel electrode should be re-dried prior to use at between 300 – 350 °C for 30 to 60 minutes. No more than four layers of electrodes should be dried at a time.
Tungsten welding rods are commonly used in gas tungsten arc welding (GTAW) or tungsten inert gas (TIG) welding. Tungsten is a rare and extremely hard metal that has the highest melting point of any metal, which makes it ideal for use in welding. Here are some reasons why someone might use tungsten welding rods:
High melting point: Tungsten has the highest melting point of any metal, which means that it can withstand high temperatures without melting or deforming. This makes it ideal for welding applications where high temperatures are required.
Non-consumable electrode: Tungsten is a non-consumable electrode, which means that it does not melt and become part of the weld. This is important in applications where the weld needs to be free from contamination.
Low thermal expansion: Tungsten has a low thermal expansion coefficient, which means that it does not expand or contract significantly when it is heated or cooled. This helps to maintain the integrity of the weld and prevents cracking or distortion.
Good conductivity: Tungsten has a high thermal conductivity, which means that it can transfer heat quickly and efficiently. This makes it ideal for welding applications where precise control of the heat input is required.
Corrosion resistance: Tungsten is highly resistant to corrosion, which makes it ideal for use in welding applications where the weld needs to be resistant to corrosion.
Overall, tungsten welding rods are preferred in applications where high-quality welds are required, and where precision and control are essential.
Thorium has slight radioactivity and emits alpha particles and occasionally some Beta and Gamma radiation. The levels are extremely low and external exposure risk is low. However, when ingested or inhaled this risk is increased.
Because welders need to grind the tips to prepare the rod for welding this creates dust particles that can be inhaled or ingested. It is recommended to wear appropriate safety gear as laid out in welding procedures.
Thoriated tungsten is recommended to be stored in a steel box.
Produced using a combination of 3 oxides: 1.5% Lanthanum, 0.08% Zirconium, 0.08% Yttrium.
PRODUCT FEATURES:
Vanguard’s welding division carries Antox and other Chemetall products. Below is a list of some of the products we carry or have access to.
The protective passive layer may be damaged during the processing of stainless steels by drilling, turning, milling, bending, welding or heat treatment. The Antox® technology ensures that your metal surfaces are protected from disturbing influences such as temperature-related oxidation and discolouration, metal deposition and organic impurities – without changing their surface structure.
Stock Vancouver Antox 71E Plus – SKU#72010002